Rotary kiln
Wolfgang Weihs
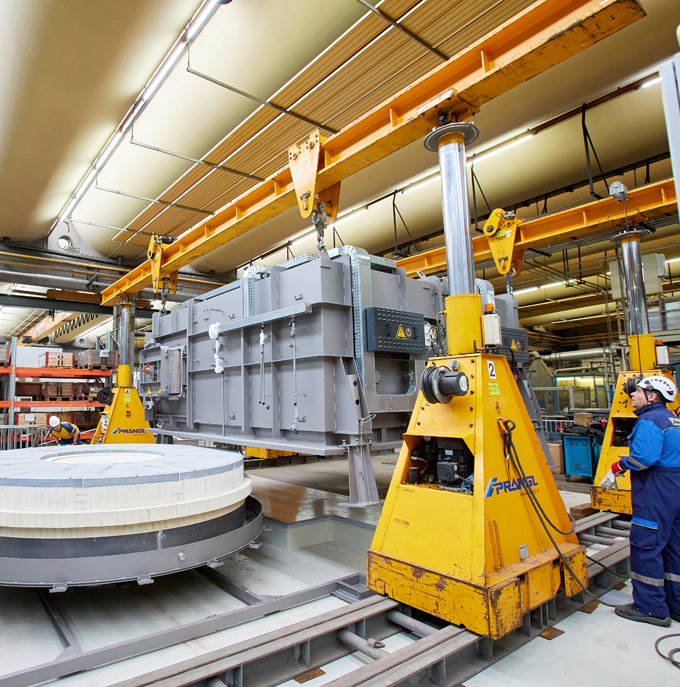
The challenge
Placement of a 10 tonne load
The delicate task for the Prangl team: A 4.4 metre high rotary kiln with a diameter of 4.0 metres was to be brought into a hall and set down there, where the 10 tonne machine was be used in the future. The challenge in this case was the fact that it was a hall equipped with production facilities and the available space was extremely limited, so ongoing operation was not to be disturbed under any circumstances.
Our solution
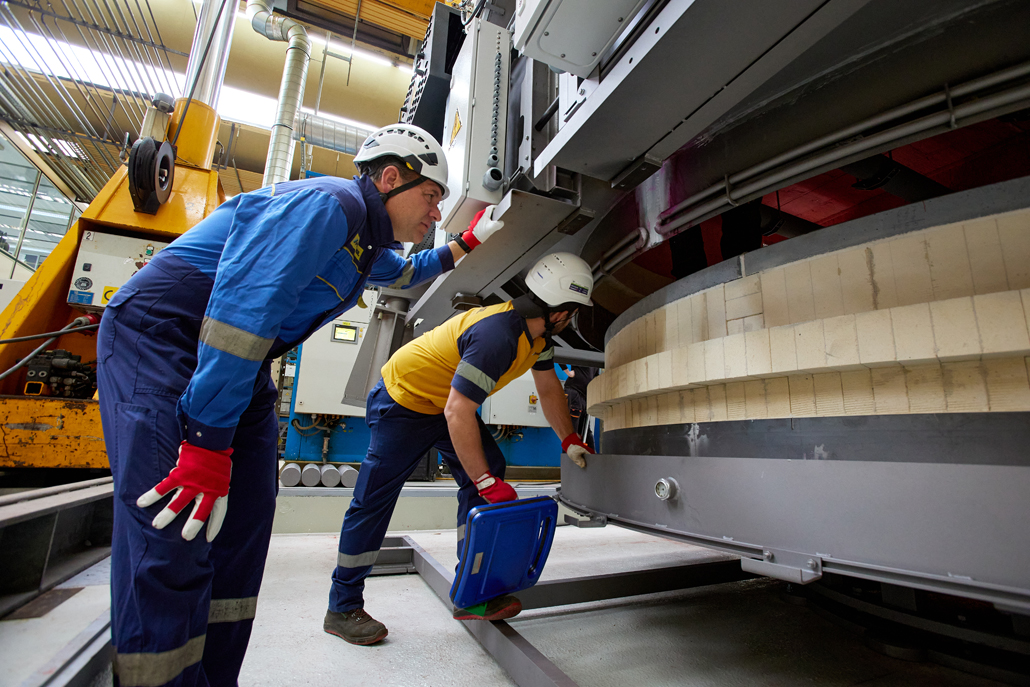
Full service package
The client - a specialist for mowing and cutting technology in agriculture and forestry - asked Prangl to put together
a full service package for this job with an indoor assignment: Unloading, insertion and final positioning of the rotary kiln in the hall. Accordingly, the selection of the necessary Prangl units was adapted to the special requirements. They had to be able to cope with the limited space available and still be able to manipulate the sometimes very heavy parts. Efficiency should not be ignored either.
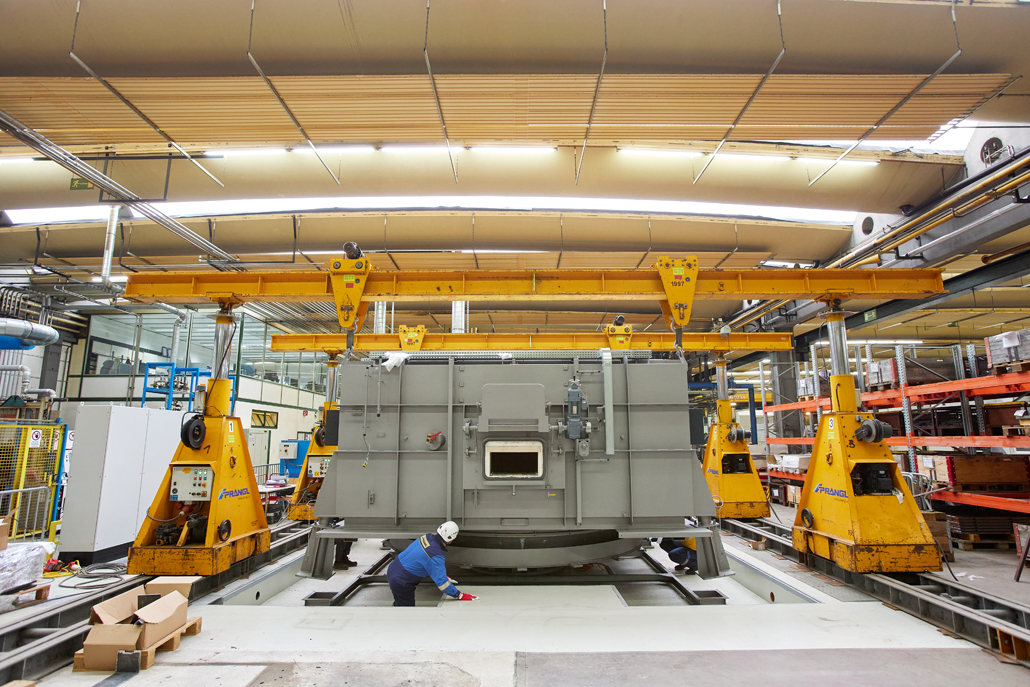
70 tonne telescopic crane, forklift truck
Due to the limited space available in the production hall, disassembly work had to be carried out in advance. Only then could the actual work begin. The first work step was carried out by a 70 tonne telescopic crane, which unloaded the delivered kiln parts from the low-loader. A forklift truck with a load capacity of 3.5 tonnes and a maximum lifting height of 4.5 metres and heavy-duty rollers were then used. Together, they had the task of bringing the individual parts into the hall and placing them at a pre-defined assembly point.
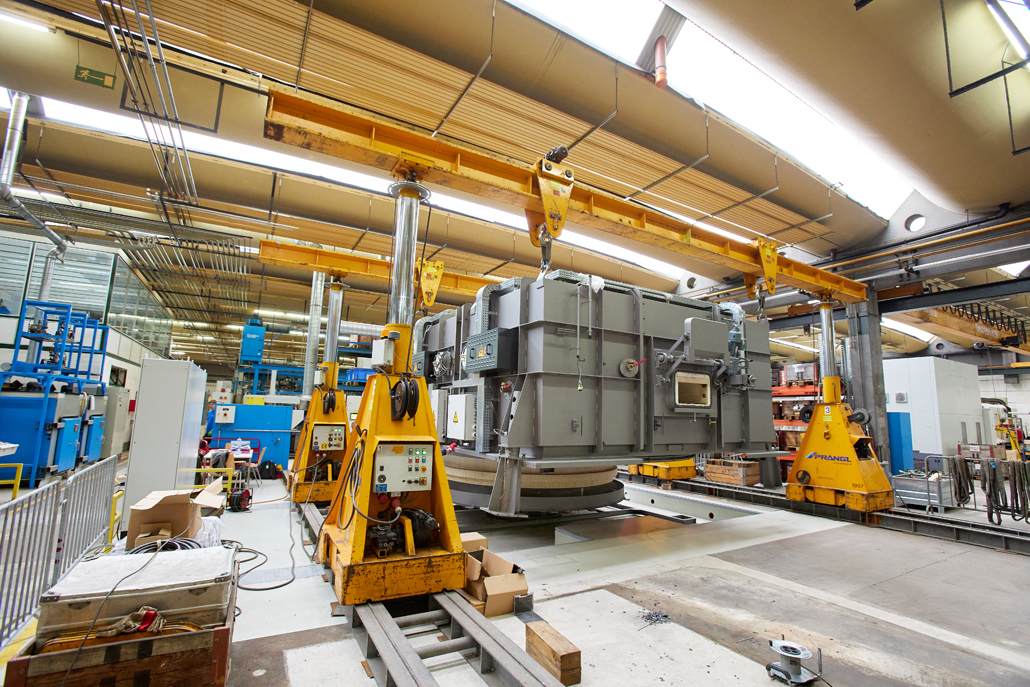
Hydraulic gantry
Due to the lack of space, a mobile crane could not be used for assembly and transport within the hall. A hydraulic gantry was therefore the perfect device for moving the rotary kiln into place. Finally, the hydraulic gantries can be combined with different dimensions and lifting capacities to suit the current situation. With multiple telescopic hydraulic jacks, a rail system, a carrier and various anchorage points, loads can be positioned with precision.
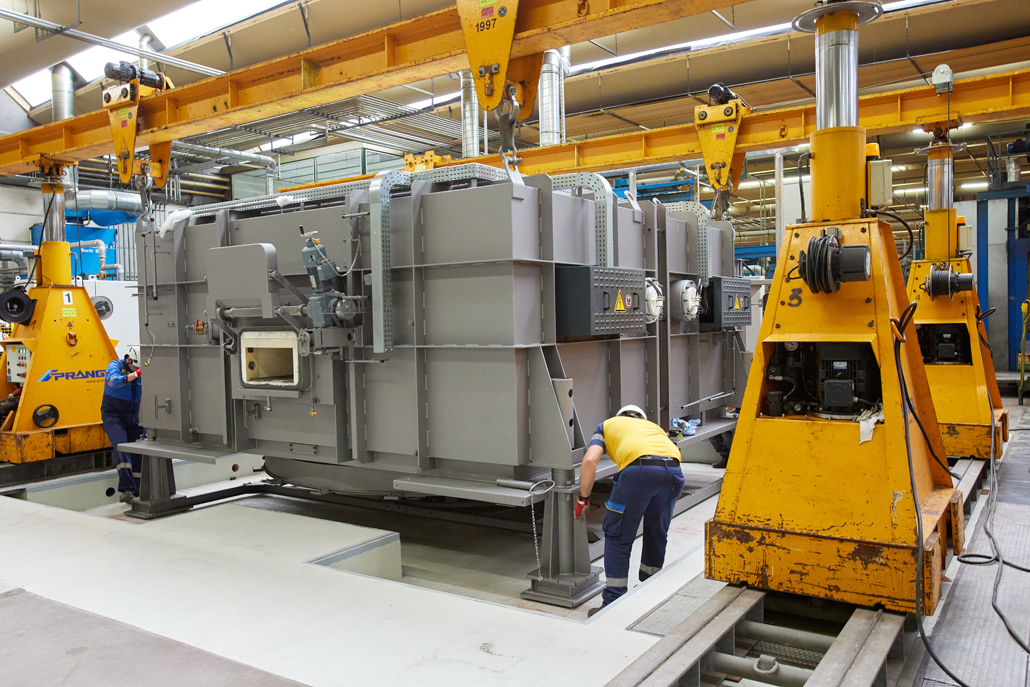
Installation of the rotary kiln
The hydraulic gantries were assembled between the assembly site and the final standing position of the kiln with the aid of the forklift. The fully assembled rotary kiln was picked up by the hydraulic gantries and was able to “float” to its destination. There, it was positioned and fitted with precision down to the last millimetre. Once the work had been successfully completed, the hydraulic gantries were disassembled again and transported away. And thanks to careful preparation and concentrated work, the Prangl team once again completed a challenging task to the client's complete satisfaction.
Industry
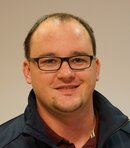